In the dynamic landscape of Industry 5.0, where intelligent manufacturing and automation drive unprecedented growth and innovation, the emergence of the Internet of Robotics Things (IoRT) stands as a revolutionary force. IoRT represents the fusion of cutting-edge technologies, including the Internet of Things (IoT), Artificial Intelligence(AI), Data Analytics, and Robotics, propelling industrial automation to new heights of efficiency and intelligence. As machines, sensors, and robots become seamlessly interconnected in an intelligent ecosystem, the manufacturing industry undergoes a profound transformation, unlocking the true potential of Industry 5.0.
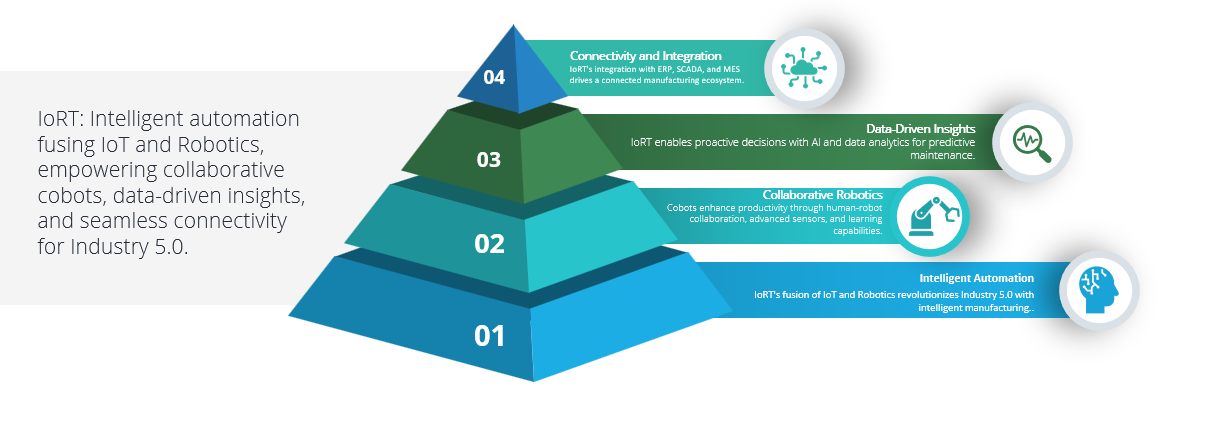
In this article, we explore the Internet of Robotics Things (IoRT) and its fusion of IoT and Robotics, revolutionizing Industry 5.0 with intelligent automation. Discover the pivotal role of collaborative robots (cobots), the power of computer vision and AI, the significance of industrial IoT and protocols, and the impact of data analytics and generative AI.
Cobots: Pioneering Collaborative Robotics
Collaborative robots, or cobots, stand at the forefront of the IoRT revolution. These robots are designed to work harmoniously alongside human operators in various industrial processes. Equipped with advanced sensors, cameras, and sophisticated software, cobots possess high perception and learning capabilities. Cobots facilitate human-robot collaboration in shared workspaces, opening new frontiers in manufacturing automation. Their applications range from assembly and packaging to quality control, ushering in a new era of efficiency and worker safety.
With several use cases possible with industrial robots, the focus of this article remains on cobots as key enablers in the industry 5.0 era, harnessing connectivity and data exchange for enhanced efficiency and worker safety.
Computer Vision and AI Empowerment
In the IoRT ecosystem, the integration of computer vision and artificial intelligence (AI) plays a transformative role. Computer vision endows robots with the ability to perceive and interpret visual information from their environment. Object detection and recognition algorithms enable cobots to identify and inspect products for defects, ensuring strict adherence to quality standards.
AI, powered by machine learning and deep learning algorithms, imbues IoRT with adaptive intelligence. Robots trained with AI can dynamically adjust their actions in response to changing conditions. They optimize their movements, predict potential bottlenecks, and make informed decisions based on real-time data, resulting in increased productivity and operational agility.
Industrial IoT: The Backbone of IoRT
At the heart of IoRT lies the Industrial Internet of Things (IIoT), where sensors and devices interconnect to gather and exchange real-time data. Sensors, such as temperature, pressure, proximity, motion, and force/torque sensors, play a pivotal role in monitoring manufacturing equipment and processes. They provide valuable insights into operational efficiency, predictive maintenance, and product quality. The IIoT enables seamless communication and collaboration between robots, sensors, and other devices, ushering in a new era of automation and intelligence.
IoT at the Edge: Empowering Real-time Decision-making
In the world of the Internet of Robotics Things (IoRT), connectivity emerges as a key enabler of smart automation and data-driven decision-making. IoT at the edge empowers real-time decision-making, reducing latency, enhancing bandwidth efficiency, and improving overall reliability.
With edge computing, IoRT systems can continue operating even in situations of intermittent or limited network connectivity, ensuring uninterrupted production and minimal disruptions. Edge computing enables sensitive data to be processed locally, reducing the risk of data exposure during transmission, thereby enhancing data privacy and security.
PLCs: Orchestrating Automation
Programmable Logic Controllers (PLCs) serve as the orchestrators of automation in the IoRT ecosystem. These rugged and flexible industrial computers act as the centralized control hub, managing and coordinating the interconnected devices, machines, and systems. PLCs provide real-time data on process status, machine performance, and equipment health, empowering decision-makers with valuable information for proactive maintenance and optimal resource allocation. Their role in seamless data exchange and communication among devices is instrumental in streamlining production workflows and achieving synchronization in complex manufacturing environments.
Sensors: Eyes and Ears of IoRT
Sensors are the eyes and ears of IoRT, enabling robots to interact with and understand their surroundings. Temperature sensors ensure optimal operating conditions, while pressure sensors monitor critical parameters in industrial processes. Proximity sensors facilitate safe and precise robot navigation, avoiding collisions with objects and humans. Motion sensors capture movement data, optimizing robot trajectories for increased efficiency. Force/torque sensors enable gentle handling of delicate components, ensuring product quality and integrity.
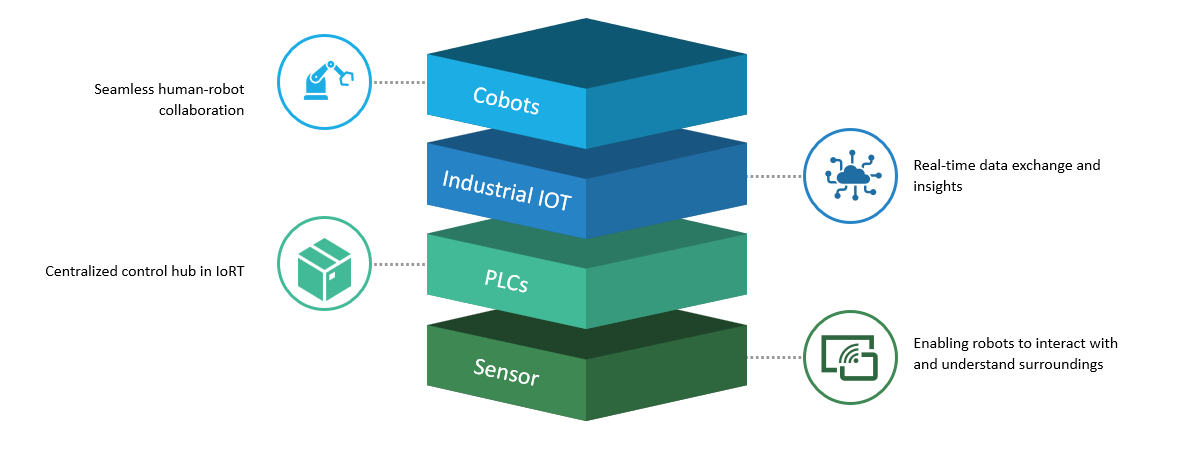
Data Analytics: Unleashing Insights from Raw Data
Data analytics is the backbone for any efficient system, transforming raw sensor data into actionable insights. Advanced algorithms and machine learning techniques analyze vast amounts of data to identify patterns, trends, and anomalies. In IoRT, data analytics facilitates predictive maintenance by detecting early signs of equipment degradation, preventing costly breakdowns and production downtime. It enables continuous process improvement by identifying bottlenecks and inefficiencies, paving the way for enhanced productivity and resource optimization.
Generative AI: Empowering Innovation in IoRT
Generative AI is a Revolutionary technology that could potentially disrupt IoRT with innovation. By leveraging existing data and patterns, generative AI creates novel designs, solutions, and optimization strategies. In the context of IoRT, generative AI can revolutionize robot design, automating robotic actions and manufacturing processes.
Integration with ERP System: Advantages for Holistic Manufacturing Management
Integrating IoRT with an Enterprise Resource Planning (ERP) system offers a holistic approach to manufacturing management. ERP systems serve as central hubs for resource planning, inventory management, and production scheduling. By connecting IoRT data with the ERP system, manufacturers gain several advantages
- Real-time Production Insights
- Optimized Inventory Management
- Enhanced Predictive Maintenance
- Seamless Production Planning
- Quality Control and Compliance
Enhancing User Experiences with HMI and User Experience Layer
Human-Machine Interaction (HMI) and User Experience (UX) play a pivotal role in maximizing the potential of IoRT. Intuitive and user-friendly interfaces enable seamless interaction between operators and robotic systems, enhancing productivity and reducing the learning curve. The integration of Augmented Reality (AR), Virtual Reality (VR), and Mixed Reality (MR) technologies enables operators to visualize and control robots, monitor operations, and receive real-time insights. A well-designed User Experience Layer ensures that data and analytics are presented in a meaningful and actionable manner, empowering decision-makers to optimize manufacturing processes and drive continuous improvements.
Integration with Existing Systems
To fully leverage the potential of IoRT, integration with existing systems is essential. Systems like SCADA (Supervisory Control and Data Acquisition) and MES (Manufacturing Execution Systems) play a vital role in industrial automation, and their integration with IoRT can enhance overall efficiency and effectiveness. SCADA systems provide real-time monitoring and control of industrial processes, while MES systems manage and optimize production workflows. By integrating IoRT data with SCADA and MES systems, manufacturers gain comprehensive insights into their operations, enabling informed decision-making and real-time adjustments to maximize productivity.
Incorporating the advancements of IoRT into existing systems empowers manufacturers to build upon their existing infrastructure and embrace the future of Industry 5.0 smart automation. The synergy of IoRT with SCADA, MES, and legacy PLCs unlocks the potential for a more connected, intelligent, and efficient manufacturing ecosystem, driving Industry 5.0 toward unprecedented levels of productivity and innovation.
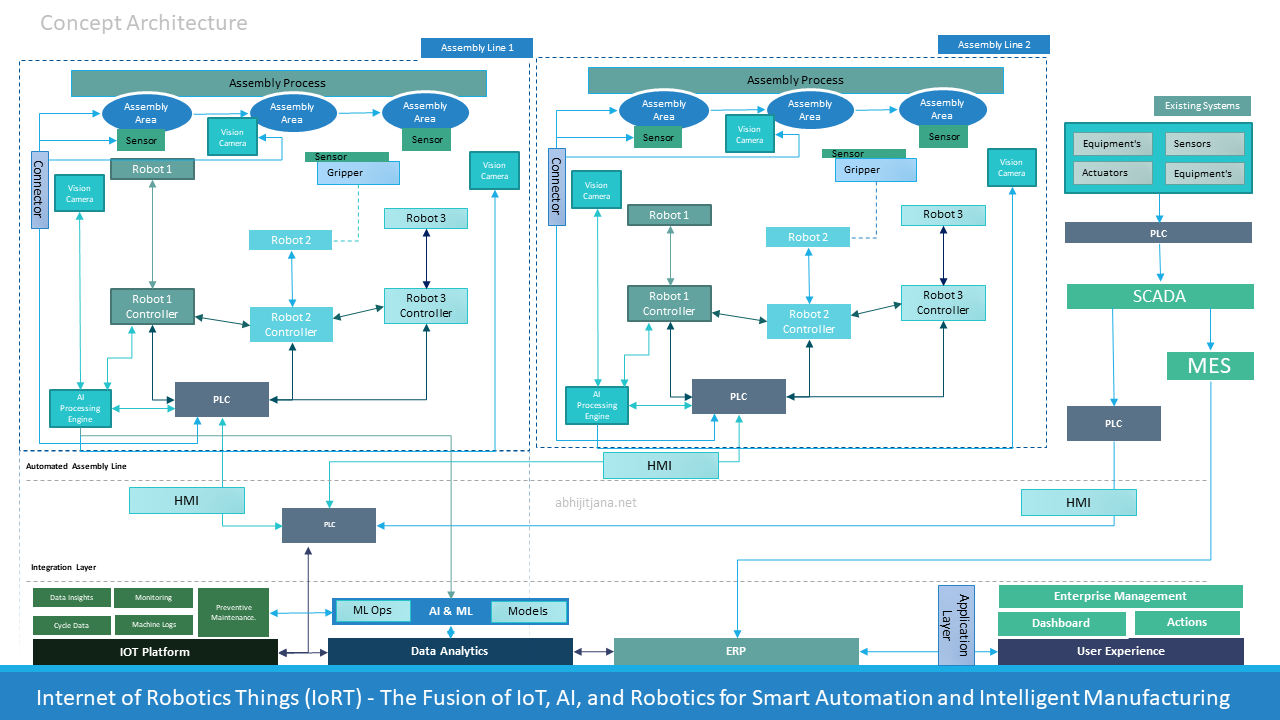
Conclusion
The Internet of Robotics Things (IoRT) heralds a transformative era in manufacturing, fusing IoT, AI, and Robotics to drive smart automation and innovation. IoRT’s seamless integration unleashes unparalleled efficiency, flexibility, and customization, paving the way for a more agile and intelligent future in manufacturing. As we embrace the synergy of IoT and Robotics, the era of smart automation powered by IoRT is set to reshape industries across the globe. Leveraging data analytics, integrating PLCs, and adopting generative AI further enhance IoRT’s potential, unlocking new possibilities for industrial automation in the Industry 5.0 era, particularly in device manufacturing using Cobots. Embracing IoT at the edge and integrating IoRT with ERP systems empowers real-time decision-making and offers a holistic approach to manufacturing management, revolutionizing the way industries operate and propel Industry 5.0 towards greater heights of productivity, efficiency, and competitiveness.